新着情報
- NEWS IT導入補助金2025 通常枠、インボイス対応類型 申請可能になりました。
- 2025.05.17 MEX金沢2025 ご来場ありがとうございました。
- 2025.04.11 設計・製造ソリューション展 名古屋 ご来場ありがとうございました。
- 2025.04.09 GW休業のお知らせをアップしました。
- 2024.12.18 冬季休業のお知らせをアップしました。
- 2024.12.13 設計・製造ソリューション展 九州 ご来場ありがとうございました。
- 2024.11.10 JIMTOF2024 ご来場ありがとうございました。
- 2024.10.04 設計・製造ソリューション展 大阪 ご来場ありがとうございました。
- 2024.07.26 工場内のシステム見える化展 ご来場ありがとうございました。
- 2024.07.24 夏季休業のお知らせをアップしました。
- 2024.07.04 ROBOT TECHNOLOGY JAPAN 2024 ご来場ありがとうございました。
- 2024.06.21 設計・製造ソリューション展 ご来場ありがとうございました。
- 2024.05.18 MEX金沢2024 ご来場ありがとうございました。
- 2024.04.12 設計・製造ソリューション展 名古屋 ご来場ありがとうございました。
- 2024.02.22 スマートファクトリーJapan ご来場ありがとうございました。
- 2024.01.26 スマート工場EXPO ご来場ありがとうございました。
メディア情報
工程管理システム
サクっと工程シリーズ
受注から出荷までガントチャートで
可視化して工程管理を効率化
納期遅延を防ぎ生産性を向上させる
工程管理システム
生産管理システム Prevision
受注生産に特化した生産管理システム
業務の一元管理による最適化で
生産計画を立てやすく
スマホ作業実績収集
「サクっとスキャン」
現場の各作業者が作業実績・不良発生を
スマホで報告
進捗管理と品質管理の負担が激減
Excel管理から脱却して事務作業も効率アップ
スマホ版工程管理システム
ガントチャート機能
工程毎に複数人がExcelで生産計画を立てていると、
前後工程の間違いなどで整合性が取れなくなり
トラブルが発生します。
これを防ぐには複数人でガントチャートを
同時編集することにより 解消ができます。
スマホ工程管理システム
サクスマ
受注・作業実績入力・作業実績修正・作業日報入力
・工程進捗問合せ・出荷が
スマホだけで操作が可能です。
急な割り込み依頼も楽勝
「生産計画システム サクっと工程SP」
自動スケジューラ「スパライシス」を使えば
急な受注の割り込み、作業遅れ、機械停止など
生産計画の障害を踏まえて自動処理し再計画
生産管理システムPrevisionで
部品欠品防止
外注加工品と購入品は現品票のバーコードを
社内加工品は作業指示書のバーコードを
読み取って
手軽に受入・作業進捗報告&部品在庫を完全管理
生産管理システムPrevisionで
有効在庫管理
現在庫の状況と出荷予定を
リアルタイムで共有・確認
在庫引当数と入荷予定数の把握で
有効在庫が一目瞭然
在庫切れを防ぎ、納期回答もスムーズ
部品表管理革命!Prevision
CSV取り込みの手間にさようなら
製作図面から作成したExcel部品表を取り込んで
資材発注も可能、発注管理がスイスイできる
スマホ仕入で作業効率化
「サクっと受入」
スマホでバーコードを読み取って楽々受入
リアルタイムで作業者と事務担当者に
情報共有可能
作業日報をなぜ提出しないの?
手書きの作業日報、
Excelでの作業日報は報告に
手間がかかり
報告漏れが発生。スマホでサクっと報告が可能
生産管理システムPrevisionで
予算・原価管理
予算内に収まるかを発注前に簡単確認
客先や仕入先との交渉もスムーズ
コスト削減と利益最大化で収益改善
生産管理システムPrevision
「部品加工原価」
作業者がスマホで作業実績をとってデータ化
部品ごと、得意先ごとに自動集計
正確な数値の把握で得意先からの
値引き交渉にも対応
PrevisionとExcelで
簡単&自由に帳票作成
生産管理システムPrevisionに
データを入力するだけで
10万件分の明細も5秒でExcel帳票に!
ほしい項目だけ自由に抽出、
帳票作成の手間が激減
フォルダー管理 prevision
図面管理システムと生産管理システムの
併用は面倒、
フォルダ管理にて一発で図面検索
スマホ版作業手順書作成システム
動画再生の環境により画質が異なります。画質が荒い場合は手動で720p以上に変更ください。
受注生産の工場向けの生産管理システムの主な機能について
- 生産管理システム内の「生産計画」とは
-
受注生産の工場においては組立業と加工業で各々の生産計画の管理の仕方が違います。
受注生産の組立業は、主に得意先の工場のライン設備などの一部の装置を得意先の納期に合わせ製造しますので設計の負荷、組立の負荷を調整した大日程計画となります。
受注生産の加工業は、機械装置を作っている工場から部品注文をもらい、依頼された納期で加工して製造しますので、自社の加工マシンが空いているか、他の受注済みの製品、部品に影響がないかを確認しながら生産計画を立てるので小日程計画となります。
- 生産管理システム内の「販売管理」とは
-
受注生産の工場では、受注してから即出荷はできないので、見積から、受注、出荷、売上までの管理については製番(個々の管理番号、製造番号)を使い個別管理をして行きます。
受注生産の組立業は、例えば1物件1000万で1か月あたり売上伝票が10件程度しか売上件数がない時がありますが、どの物件(製番)に入金があったのかなど入金については個別の入金管理が必要になります。
受注生産の加工業は、1か月1000件など売上件数が多いので、納期遅れしないように工程管理、出荷管理と複数製番の配送をまとめ納品、売上するなどを考慮する必要があります。
得意先からの検収明細書が送られてくるケースがあり、自社の請求と検収明細書の突合せも必要になります。
- 生産管理システム内の「購買管理」とは
-
受注生産の組立業では、設計から出図された部品表に基づき手配を行います。部品点数が1000件などで部品点数が非常に多いので、発注前の金額交渉、納期確認、入荷された時の受入確認が必要です。組立するときに欠品となると組立待ち、製品納期遅れの原因となるので、購入部品、外注加工部品の進捗管理が重要です。
受注生産の加工業は、主に材料と外注、工具などの消耗品になります。工程途中の外注、表面処理などが管理できてないと納期遅れの原因となります。
- 生産管理システム内の「工程管理」とは
-
受注生産の組立業は、上記の生産計画と同様にまずは、大日程計画が必要で設計の納期管理、組立前の部品進捗管理が必要になります。
受注生産の加工業は、納期遅れ防止ために加工工程の進捗管理、効率生産のためのマシン毎の負荷調整が必要になります。マシンの負荷調整については、個々の部品の工程ごとの加工時間が把握できてないと負荷調整ができません。
- 生産管理システム内の「作業実績収集」とは
-
受注生産の組立業は、設計、組立者などの作業日報管理が必要になります。下記の原価集計のひとつの要素になるので作業日報の習慣づけが必要になります。
受注生産の加工業は、開始時、終了時のバーコードとタブレットなどで作業工数の把握、完了日時の把握をする実績収集が一般的にですが、IOT連携などでマシンから自動で作業実績を収集するケースもあります。
- 生産管理システム内の「在庫管理」とは
-
受注生産の組立業は、納期がかかる部品などを在庫します。
在庫された部品は受注時に部品を引当てて組立前に在庫払出をして使用します。その時に下記の原価機能と関連しますが、在庫部品の原価振替が必要になります。
受注生産の加工業は、主に製品在庫の管理となります。前回余分に製作した製品在庫を引当てるなど余分な在庫を作らない製品在庫管理が必要になります。
- 生産管理システム内の「原価管理」とは
-
受注生産の組立業は、設計段階でのコストダウン検討、発注前のコストダウン検討、予算管理と実際原価の管理が必要になり粗利の確保が重要になります。
受注生産の加工業は、各部品、製品の工程ごとの予定時間と、作業時間の把握により若手作業者の育成、ベテラン作業者のノウハウ共有、継承などによりコストダウンが必要になります。
ワンポイントアドバイス
IT導入補助金2025について
イベント情報
-
2025年7月9日~7月11日
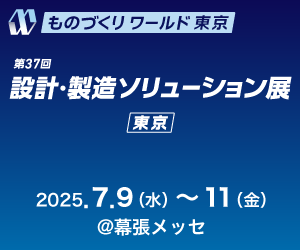
ご来場お待ちいたしております
-
2025年5月15日~5月17日
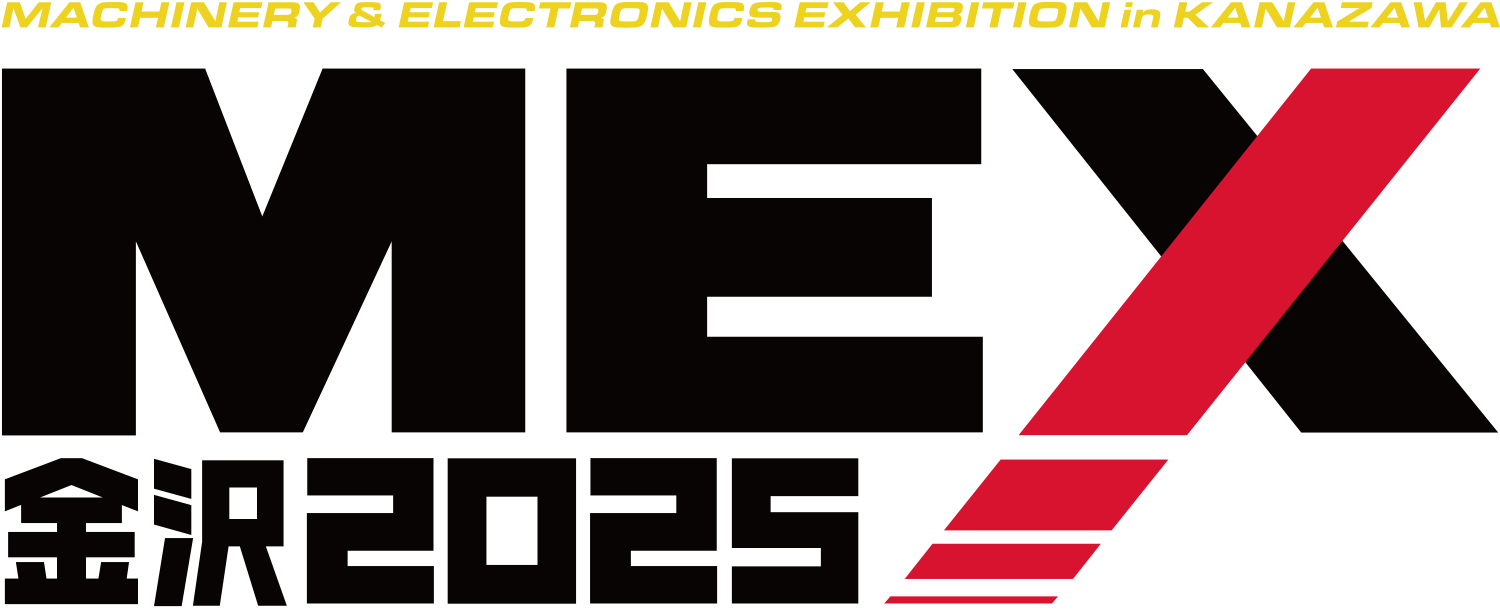
ご来場ありがとうございました
-
2025年4月9日~4月11日
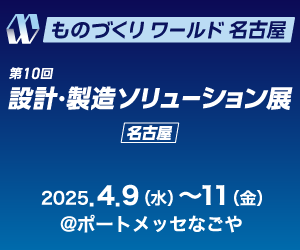
ご来場ありがとうございました
-
2024年12月11日~12月13日
![設計・製造ソリューション展[九州]](event/images/2024kyushuDMS.png)
ご来場ありがとうございました
-
2024年11月5日~11月10日
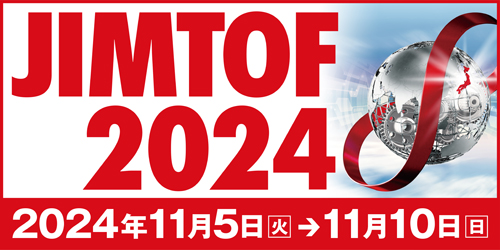
ご来場ありがとうございました
-
2024年10月2日~10月4日
![設計・製造ソリューション展[大阪]](event/images/2024osakaDMS.png)
ご来場ありがとうございました
-
2024年7月24日~7月26日
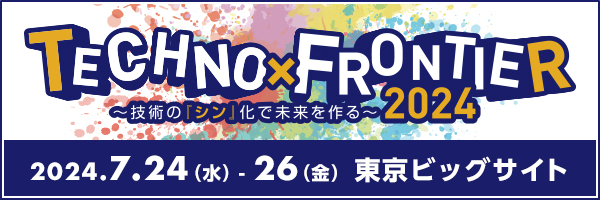

ご来場ありがとうございました
-
2024年7月4日~7月6日
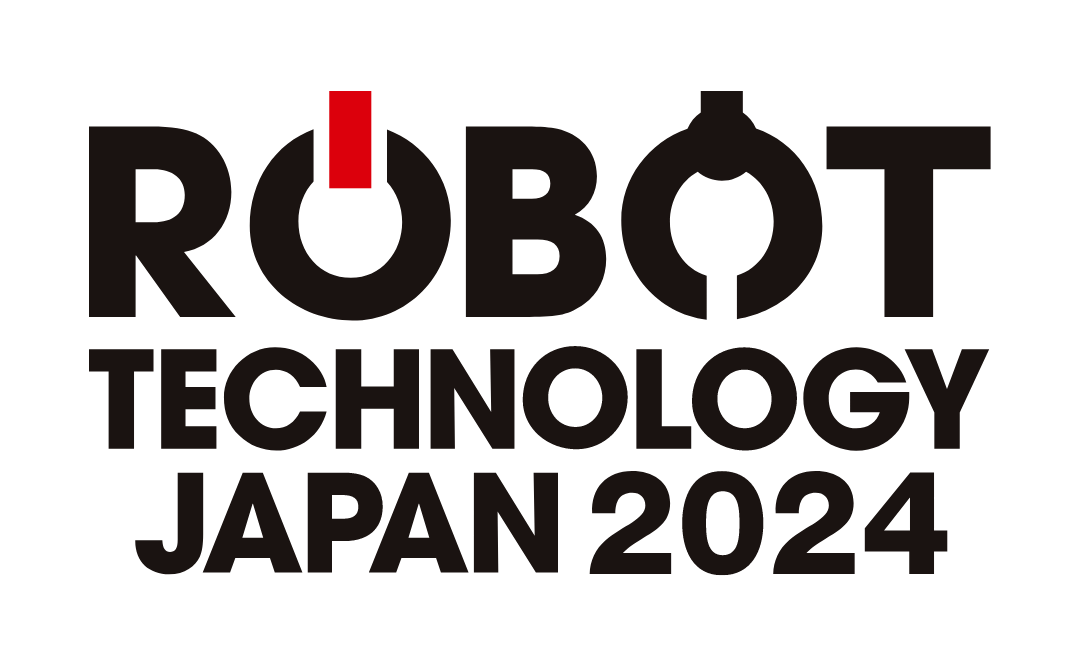
ご来場ありがとうございました
-
2024年6月19日~6月21日
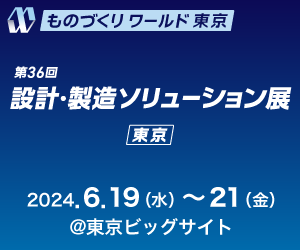
ご来場ありがとうございました
-
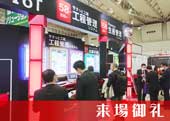
会場の様子はこちら
-
おかげさまでユーザー数 450社
このサイトはリンクフリーです。
貴社の生産管理情報の一つとしてお使い下さい。